鑄造是國民經濟重要的基礎工業之一,但鑄造 過程的控制、設計及工藝流程往往依賴于經驗判斷, 因而鑄件的質量不易保證,廢品率較高。壓力鑄造 是特種鑄造的一種,其實質是液態或者半液態金屬 在高壓力作用下,以較高的速度充填型腔,并在壓力 作用下凝固而獲得鑄件的一種方法。要獲得高質 量、高水平壓鑄件,使壓鑄件達到光潔、輪廓清晰、組 織致密、強度高的要求,需要對壓鑄過程中各影響因 素進行協調統一。對于鋁合金壓鑄件,從生產準備 到批量生產,牽涉的環節很多,影響因素也很多,包 括材質、模具、設備、工藝等各方面。
1 壓鑄鋁合金的分類及性能
壓鑄鋁合金有良好的使用性能和工藝性能,因 此鋁合金的壓鑄發展迅速,在各個工業部門中得到 廣泛的應用,用量遠遠高于其他有色合金,在壓鑄生 產中占有極其重要的地位。按所含基本元素可將鑄造鋁合金分為Al-Si合金、Al-Cu合金、Al-Mg 合 金、Al-Zn合金。
1. 1 Al-Si合金
由于共晶Al-Si合金具有結晶溫度間隔小、合 金中硅相有很大的凝固潛熱和較大的比熱容、其線 收縮系數也比較小的特點,因此其鑄造性能一般要 比其他鋁合金的好,其充型性能也好,熱裂、縮松傾 向比較小。Al-Si共晶體中所含的脆性相(硅相) 數量最少,質量分數僅為 10% 左右,因而其塑性比 其他鋁合金好,組織中僅存的脆性相還可通過變質 處理降低其脆性。實驗表明Al-Si共晶體在其凝 固點附近溫度仍保持良好的塑性,這是其他鋁合金 所沒有的。
鑄造合金組織中常要有相當數量的共晶體,以 保證其良好的鑄造性能;共晶體數量的增加又會使 合金變脆而降低力學性能,兩者之間存在一定的矛 盾。但是由于Al-Si共晶體有良好的塑性,能較好地兼顧力學性能和鑄造性能兩方面的要求,所以Al-Si合金是目前應用最為廣泛的壓鑄鋁合金。
我國壓鑄鋁合金品種中,絕大多數以Al-Si合 金為主,這類合金存在強度較低、切削性能不夠好、 螺紋加工困難等現象,所以近年來我國正在開發高 強度合金。
在美國的高強度Al-Si-Cu合金(SC84A、SC114A、SC84B、SC102A)中銅的質量分數為 2.0% ~4.0%,鋅的質量分數不超過3%,硅的質量分數 為7.5% ~12.0%(具體見表1),具有較高的力學性 能、良好的壓鑄工藝性能和機械加工性能。近年 來我國研究的Al-Si-Cu新型高強度鋁合金有 YL112、YL113、YL117 等。
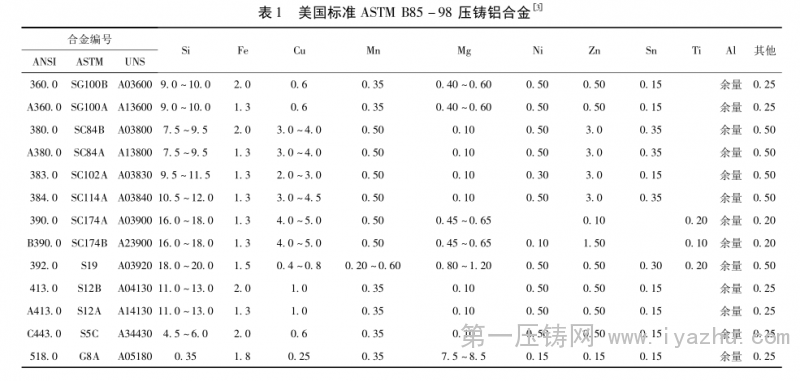
1. 2 Al-Mg合金
Al-Mg合金的性能特點是:室溫力學性能好; 抗蝕性強;鑄造性能比較差;力學性能的波動和壁厚 效應都比較大;長期使用時,有因時效作用而使合金 的塑性下降,甚至壓鑄件出現開裂的現象;壓鑄件產 生應力腐蝕裂紋的傾向也較大等。Al - Mg 合金的 缺點部分抵消了它的優點,使其在應用方面受到一 定的影響。
1. 3 Al-Zn合金
Al-Zn合金壓鑄件經自然時效后,可獲得較高 的力學性能。當其鋅質量分數大于10% 時,強度顯 著提高。此合金的缺點是耐腐蝕性差,有應力腐蝕 的傾向,壓鑄時易熱裂。常用的Y401合金流動性 好,易充滿型腔,缺點是形成氣孔的傾向性大,硅、鐵 含量較少時,易熱裂。
1. 4 特殊性能的壓鑄鋁合金
國內外研制的特殊性能的壓鑄鋁合金有:
裝飾型Al-Mn合金:適用于陽極氧化處理和 著色處理,伸長率高,還具有相當的耐蝕性。但其強 度不高,收縮率大,易粘模。
熱處理型Al-Si-Cu合金:可進行淬火后不完 全人工時效和淬火后完全人工時效至最大硬度。
此外還有表面處理和熱處理復合型的Al-Mn-Zn合金、耐磨型過共晶Al-Si合金和防爆防振型Al-Zn合金等。另外還有壓鑄鋁合金復合材料,目 前尚未普遍生產與應用。
2 壓鑄件的氣孔缺陷及產生原因
鋁合金壓鑄生產的工件常因氣孔存在而導致報 廢,產生氣孔的原因很多,在解決這一產品質量問題 時常常無從下手,如何快速、正確地采取措施減少因 氣孔而造成的廢品率,這是各鋁合金壓鑄廠家所關 注的問題。
在鋁合金壓鑄生產中,依氣孔產生的原因,常有 如下幾類。
2. 1 精煉除氣質量不良產生的氣孔
在鋁合金壓鑄生產中,熔化了的鋁液澆注溫度 一般常在610~660℃,在此溫度下,鋁液中溶解有 大量的氣體(主要是氫氣),鋁合金氫氣的溶解度與 鋁合金的溫度密切相關,在660℃左右的液態鋁液 中約為0.69cm3/100g,而在660℃左右的固態鋁合 金中僅為0.036cm3/100g,此時液態鋁液中含氫量 約為固態的 19 ~20 倍。所以當鋁合金凝固時,便有 大量的氫析出以氣泡的形態存在于鋁合金壓鑄件 中。
減少鋁液中的含氣量,防止大量的氣體在鋁合 金凝固時析出而產生氣孔,這就是鋁合金熔煉過程 中精煉除氣的目的。如果在鋁液中本來就減少了氣 體的含量,那么凝固時析出氣體量就會減少,因而產 生的氣泡也顯著減少。因此,鋁合金的精煉是非常 重要的工藝手段,精煉質量好,氣孔必然少,精煉質 量差,氣孔必然多。保證精煉質量的措施是選用良 好的精煉劑,良好的精煉劑是在660℃ 左右可以起 反應產生氣泡,所產生氣泡不太劇烈,而是均勻不斷 的產生氣泡,通過物理吸附作用,這些氣泡與鋁液充 分接觸,吸附了鋁液中的氫將其帶出液面。因此冒 泡時間不宜過短,一般要有6~8min的冒泡時間。
當鋁合金冷卻到300℃時,氫在鋁合金中的溶 解度僅為0.001cm3/100g以下,此時僅為液態時的1/700,這種凝固后氫氣析出而產生的氣孔是分散 的,細小的針孔,這不影響漏氣和加工表面,肉眼基 本看不見。
在鋁液凝固時因氫氣析出所產生的氣泡比較 大,多在鋁液最后凝固的心部,雖然也分散,但這些 氣泡常常導致滲漏,嚴重時常導致工件報廢。
2. 2 因排氣不良產生的氣孔
在鋁合金壓鑄中,因模具的排氣通道不暢,模具 排氣設計結構不良,壓鑄時型腔內的氣體無法完全 順暢排出,造成在產品某些固定部位存在氣孔。這 種由模具型腔中氣體形成的氣孔時大時小,氣孔的 內壁呈鋁與空氣氧化的氧化色,與氫氣析出產生的 氣孔不同,氫氣析出氣孔內壁不如空氣孔光滑,沒有 氧化色,而是灰亮的內壁。對于因排氣不良而產生 的氣孔,應改進模具的排氣通道,及時清理模具排氣 通道上的殘留鋁皮就可以避免。
2. 3 因壓鑄參數不當造成卷氣產生的氣孔
在壓鑄生產中壓鑄參數選擇不當,鋁液壓鑄充 型速度過快,使型腔中氣體不能完全及時平穩的擠出型腔,而被鋁液的液流卷入鋁液中,因鋁合金表面 快速冷卻,被包在凝固的鋁合金外殼中,無法排出形 成了較大的氣孔。這種氣孔往往在工件表面之下, 鋁液進口比最后匯合處少,呈梨形或橢圓狀,在最后 凝固處又多又大。對于這種氣孔應調整充型速度, 使鋁合金液流平穩推進,不產生高速流動而卷氣。
2. 4 鋁合金的縮氣孔
鋁合金同其它材料一樣,在凝固時產生收縮,鋁 合金的澆鑄溫度愈高,這種收縮就愈大,單一的因體 積收縮產生的氣孔是存在于合金最后凝固部位,呈 不規則形狀,嚴重時呈網狀。往往在產品中,它與凝 固時因氫氣析出的氣孔同時存在,在氫析出氣孔或 卷氣孔的周圍存在縮氣孔,在氣泡周圍有伸向外部 的絲狀或網狀氣孔。
對于這種氣孔,應從澆鑄溫度著手解決,在壓鑄 工藝條件允許的情況下,盡量降低壓鑄時的鋁液澆 鑄溫度。這樣可以減少鑄件的體積收縮,減少縮氣 孔及縮松。如果常在加熱部位出現這種氣孔,可以 考慮增加抽芯或冷鐵,使其改變最后凝固部位,解決 滲漏缺陷問題。
2. 5 因產品壁厚差過大而引起的氣孔
產品形狀常有壁厚差過大問題,在壁厚中心是 鋁液最后凝固的地方,也是最易產生氣孔的部位,這 種壁厚處的氣孔是析出氣孔和收縮氣孔的混合體, 不是一般措施所能防止的。
對產品的形狀在設計時就應考慮盡量減少壁厚 不均勻,或過厚的問題,采取空心結構,在模具設計 上應考慮增設抽芯或冷鐵,或水冷,或增加模具此處 的冷卻速度。在壓鑄生產中,要注意厚度大部位的 過冷量,適當降低澆注溫度等。
從上述氣孔的分類可知,在鋁合金壓鑄生產中 產品產生氣孔的原因很多,必須找出原因對癥下藥 才能解決問題。防止氣孔的措施和途徑主要有:
(1)保證鋁合金熔煉的精煉除氣質量,選用好 的精煉劑、除氣劑,減少鋁液中的含氣量,及時清除 液面浮渣、泡子之類氧化物,防止再次帶入氣體進入 壓鑄件中。
(2)選擇良好的脫模劑,所選用的脫模劑應是 在壓鑄中不產生氣體的,又有良好脫模性能的。
(3)保證模具排氣通暢不堵死,排氣順暢,保證 模具中的氣體完全排出,尤其是在鋁液最后聚合處 排氣通道必須通暢。
(4)調整好壓鑄參數,充型速度不可過快,防止卷氣。澆鑄溫度也要控制好。
(5)產品設計和模具設計中應注意抽芯和冷卻 的使用,盡量減少壁厚差過大。
(6)對常在固定部位出現的氣孔,應從模具和 設計上改善。
3 鋁合金壓鑄技術的新發展
近年來,人們為了解決壓鑄件內部存在的氣孔 和縮孔問題,使之能生產出高強度、高致密性、可焊 接、能進行熱處理、可扭曲等各種性能的壓鑄件,在 繼續完善真空壓鑄以外又發展了擠壓鑄造和半固態 壓鑄等新技術,并概括地稱之為“高密度壓鑄法”。
3. 1 真空壓鑄技術
真空壓鑄法是將型腔中的氣體抽空或部分抽 空,降低型腔中的氣壓,以利于充型和排除合金熔體 中的氣體,使合金熔體在壓力作用下充填型腔,并在 壓力下凝固而獲得致密的壓鑄件。
3. 2 充氧壓鑄技術
壓鑄件中的氣體絕大部分為 N 2 和 H 2 ,幾乎沒 有 O 2 ,主要原因是 O 2 與活性金屬發生反應生成了 固體氧化物,這為充氧壓鑄技術提供了理論基礎。 充氧壓鑄是在壓鑄前將氧氣充入型腔,取代其中的 空氣。當進入型腔時,一部分氧氣從排氣槽排出,殘 留的氧與金屬液發生反應,生成彌散狀的氧化物微 粒,在鑄型內形成瞬間真空,從而獲得無氣孔的壓鑄 件。
3. 3 半固態壓鑄技術
半固態壓鑄是在液態金屬凝固時進行攪拌,在 一定冷卻速度下獲得約 50% 甚至更高固相組分的 漿料,然后通過壓鑄使漿料成形的技術。目前,半固 態壓鑄有兩種工藝:即流變成形工藝和觸變成形工 藝。前者是將液態金屬送入特殊設計的壓射成形機 筒中,由螺旋裝置施加剪切使其冷卻成半固態漿料, 然后進行壓鑄。后者是將固態金屬粒或碎屑送入螺 旋壓射成形機中,在加熱和受剪切的條件下使半固 態金屬顆粒經壓鑄成形。
3. 4 擠壓壓鑄技術
擠壓壓鑄又稱“液態金屬模壓”。其鑄件致密 性好,力學性能高,且無澆冒口。我國一些企業已將 其應用于實際生產中。擠壓壓鑄技術具有極好的工 藝優勢,它不僅能替代傳統的壓鑄、擠壓鑄造、低壓 鑄造、真空壓鑄工藝,還能對差壓鑄造、連鑄連鍛、半固態流變鑄造工藝進行兼容。專家認為,擠壓壓鑄 技術是一項前沿性的新技術,橫跨多個工藝領域,內 涵豐富,創新性強,極具挑戰性。
3. 5 電磁泵低壓鑄造技術
電磁泵低壓鑄造是一種新崛起的低壓鑄造工 藝,同氣體式低壓鑄造技術相比,在加壓方式方面與 其完全不同。其采用非接觸式的電磁力直接作用于 液態金屬,大大降低了由于壓縮空氣不純及分壓過 高所帶來的氧化和吸氣等問題,實現了鋁液的平穩 輸送和充型,可防止由于紊流造成的二次污染。另 外電磁泵系統完全采用計算機數字元控制,工藝執 行非常準確、重復性好,使這種工藝在成品率、力學 性能、表面質量和金屬利用率等方面都具有明顯優 勢。隨著研究的不斷深入,這項工藝也愈來愈成熟。
4 結 語
鋁合金圓盤、圓筒壓鑄件由于其壁厚不均勻,容 易產生氣孔和縮氣孔等壓鑄質量缺陷。通過不斷的 澆注試驗,工程師可以尋求更優化的壓鑄工藝參數。 這樣既能選擇合理的工藝參數,又能避免實際澆鑄 的成本浪費,為企業帶來顯著的經濟效益。希望通 過本課題能對實際生產有一定幫助,最終的目的是 生產出合格的壓鑄件,滿足企業實際生產的需求。 從近年來的國內外壓鑄研究來看,隨著理論研究方 面工作的更加深入,尤其是計算機模擬技術的發展, 使金屬在填充型腔的流動形態、金屬在型腔中的凝 固過程、型腔內金屬液體的流動壓力、模具的溫度梯 度、模具的變形等方面有很大的理論突破。
本文出自輕 金 屬 2012年11期 作者:向 東,陳 晉
- 上一條: 鋁合金真空壓鑄與普通壓鑄的區別?
- 下一條: 鋅合金壓鑄件最常見的缺陷分析